T-SHIRT PRINTING
HIGHEST QUALITY SERVICE
T-SHIRT PRINTING
HIGHEST QUALITY SERVICE
T-SHIRT AND GARMENT PRINTING OPTIONS
Whatever your artwork, garments type, material or desired result, we have all the best possible garment and t-shirt printing solutions here at 3rd Rail. We don’t expect you to know what print type will best serve your needs as we are more than happy to guide you in the right direction, but if you want to know a little more here is some information about the different garment printing options available.
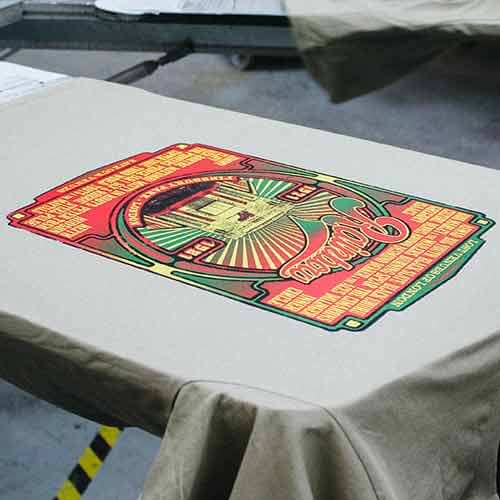
SCREEN PRINTING
Screen printing for t-shirt printing offers vibrant, durable, and customized designs. It’s cost-effective for bulk orders, provides versatility in materials and colors, and ensures consistency, making it an ideal choice for personalized, long-lasting apparel.
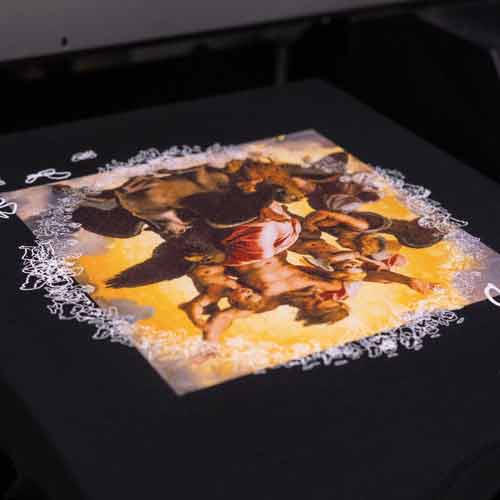
DTG PRINTING (DIGITAL)
Direct-to-Garment (DTG) printing for t-shirt customization offers vibrant, detailed, and full-color prints. It’s perfect for small batches and intricate designs, with minimal setup costs. DTG is an eco-friendly choice, as it uses water-based inks, making it a versatile and sustainable option for custom apparel.
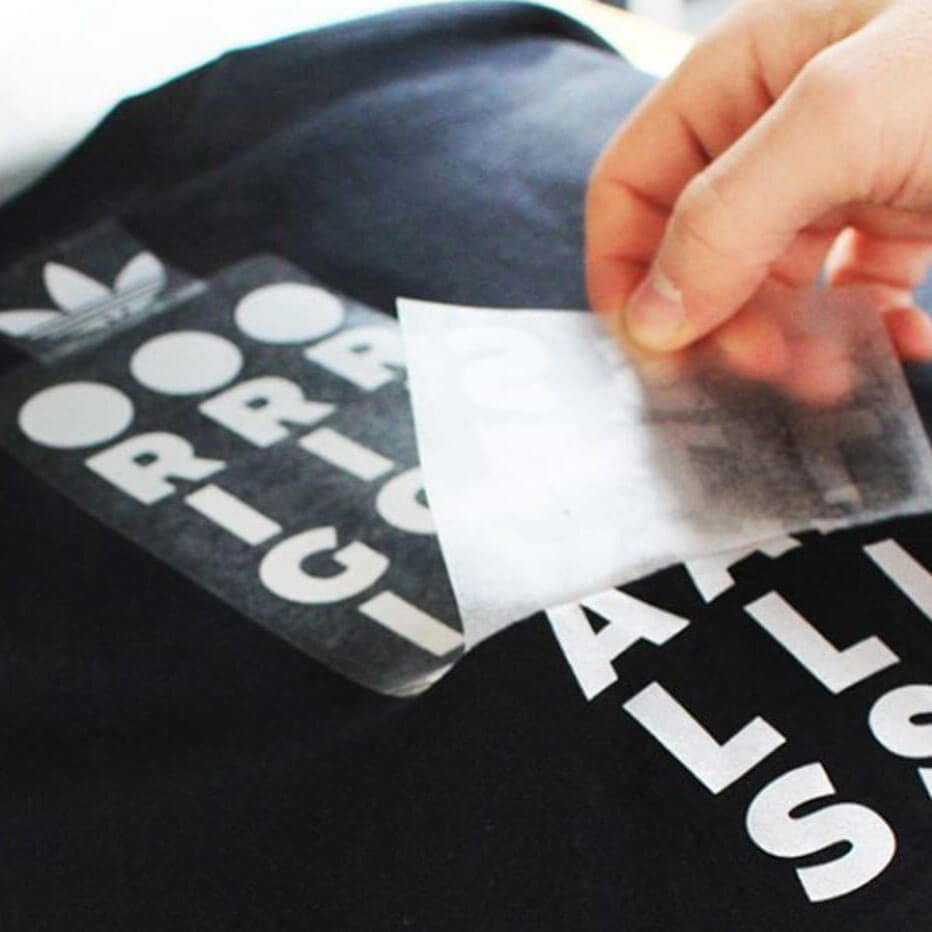
VINYL TRANSFER
Vinyl printing for t-shirt customization provides sharp, durable designs in a wide range of colors. It’s ideal for text and simple graphics, with long-lasting results that resist fading. Vinyl is cost-effective for small orders and offers a smooth, glossy finish.
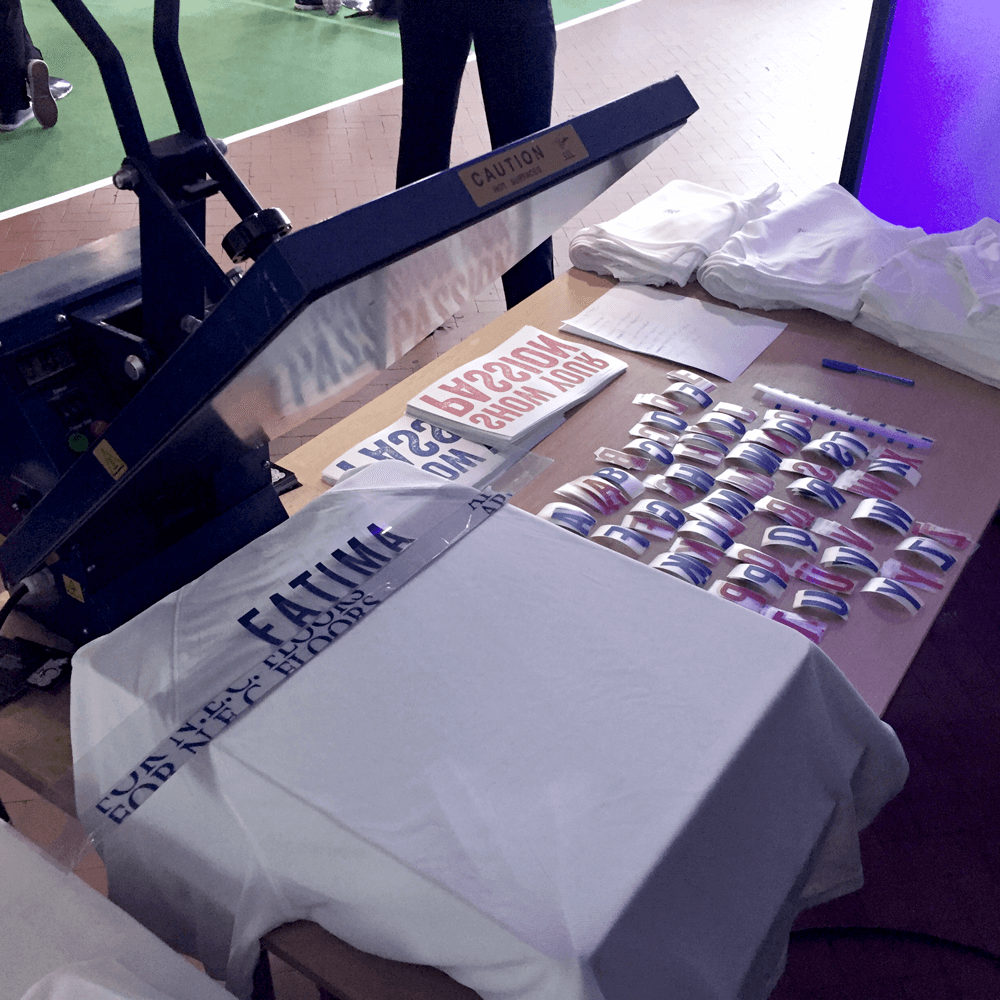
DTF PRINTING
Direct-to-Film (DTF) printing for t-shirt customization offers vibrant, high-resolution prints on various fabrics, including polyester. It’s cost-effective for small and large orders, durable, and eco-friendly. DTF technology ensures detailed and long-lasting designs with a soft touch.
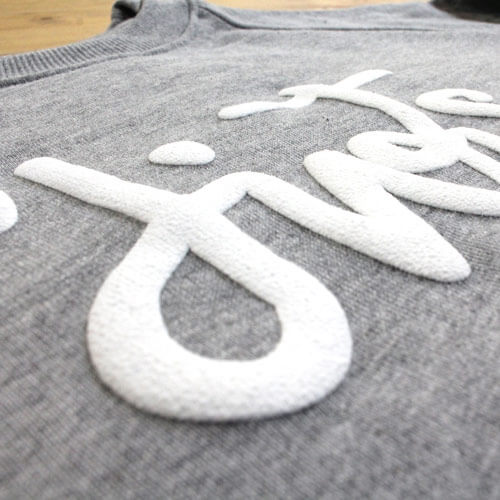
SPECIALITY INKS
Screen printing boasts a wide array of specialty inks that enhance design possibilities. From shimmering metallics to glow-in-the-dark and even puff inks for textured effects, these inks allow for unique, eye-catching designs on garments and promotional items.
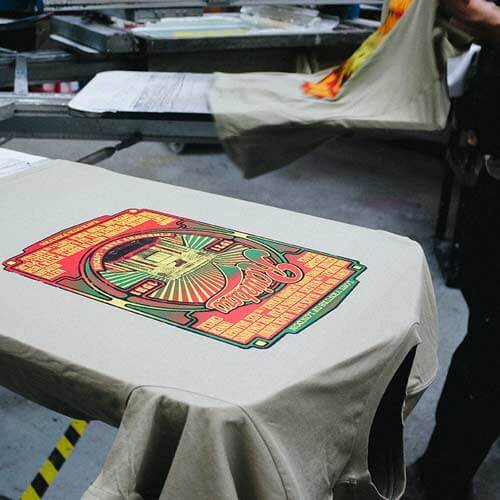
BULK PRINTING
Screen printing stands out as the premier choice for bulk t-shirt printing. It offers unparalleled cost-efficiency for large quantities, ensuring consistent quality and custom branding, resulting in significant cost savings per unit.
SCREEN PRINTING INK TYPES
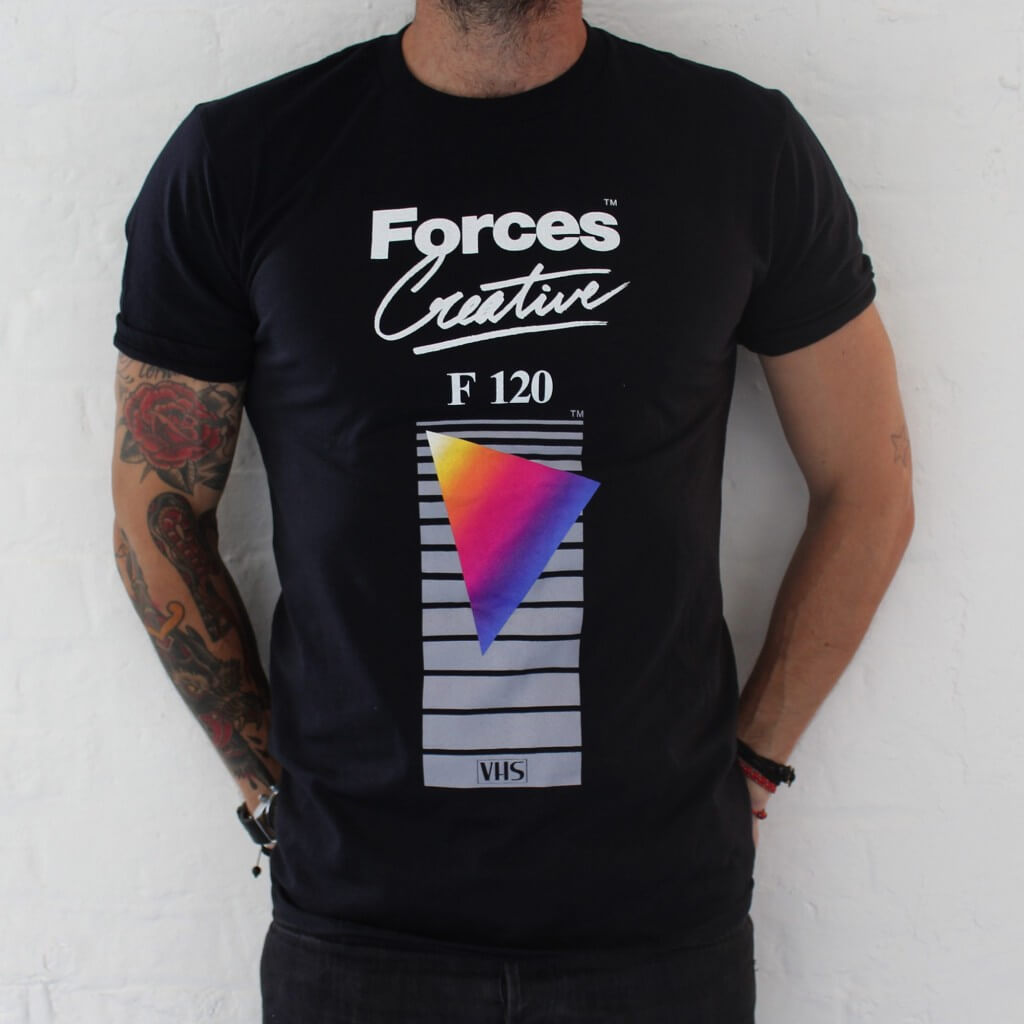
PLASTISOL INK
This is an oil based ink that was purposely created for t-shirt printing. It’s great if you want bright, solid colours that will barely ever fade. Plastisol also wins every time for tonal designs and can retain very fine detail, even over large week long print runs.
The main drawback is that it’s not as breathable and heavier to wear than its water based or discharge counterparts.
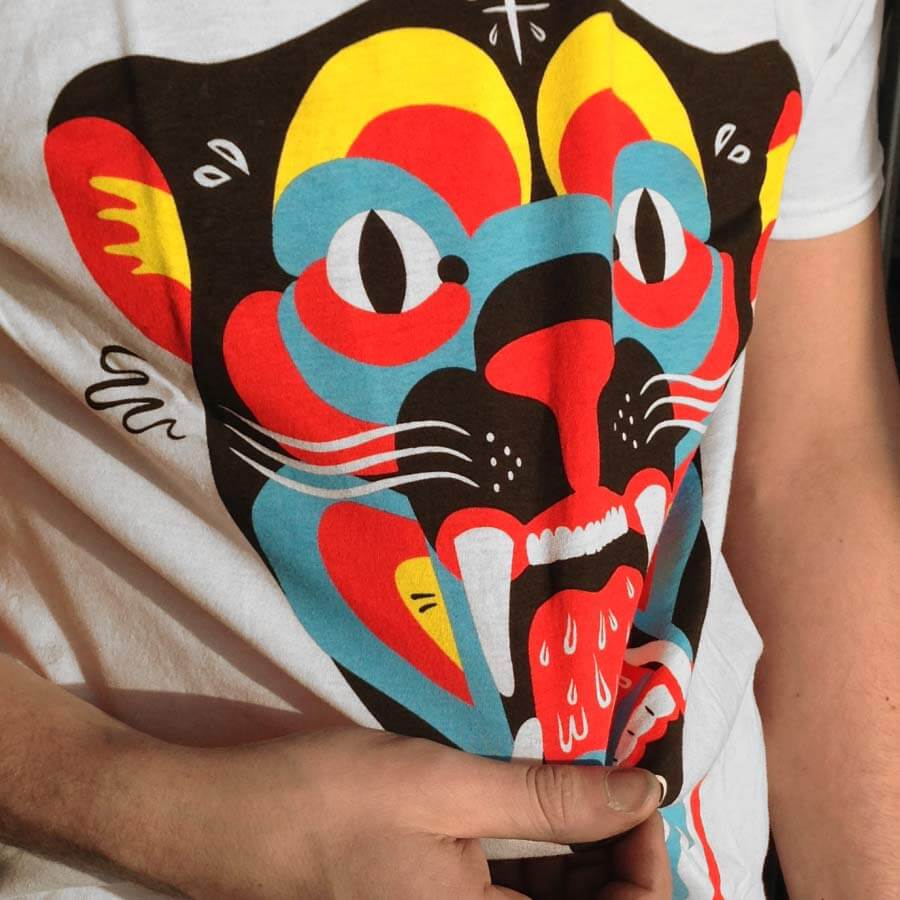
WATER BASED INK
Often the best choice on light garments the ink really penetrates the fabric leaving a non-glossy, super soft, almost textureless finish. It’s also the most ecological choice.
A downside is the colours will not stay box-fresh bright after washing and won’t show up well on darker fabrics. The ink is also prone to drying out during the run which may lead to inconsistencies.
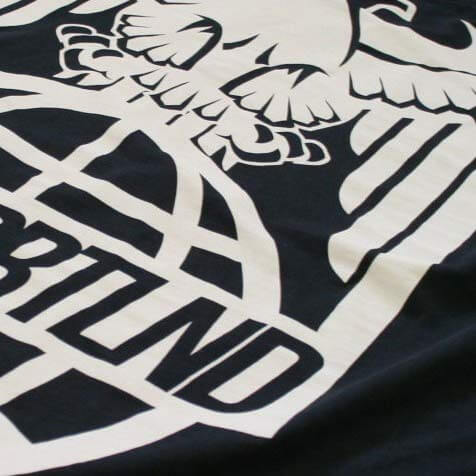
DISCHARGE INK
We add a bleach based additive to the ink, print it like normal onto dark fabric and pop it into the dryer. The heat activates the bleach taking the printed areas back to their natural, un-dyed colour thus allowing the pigments in the ink to stand out.
This is our ‘go to’ for large, soft prints onto dark garments. However the effect will not work fully unless the material is 100% cotton.
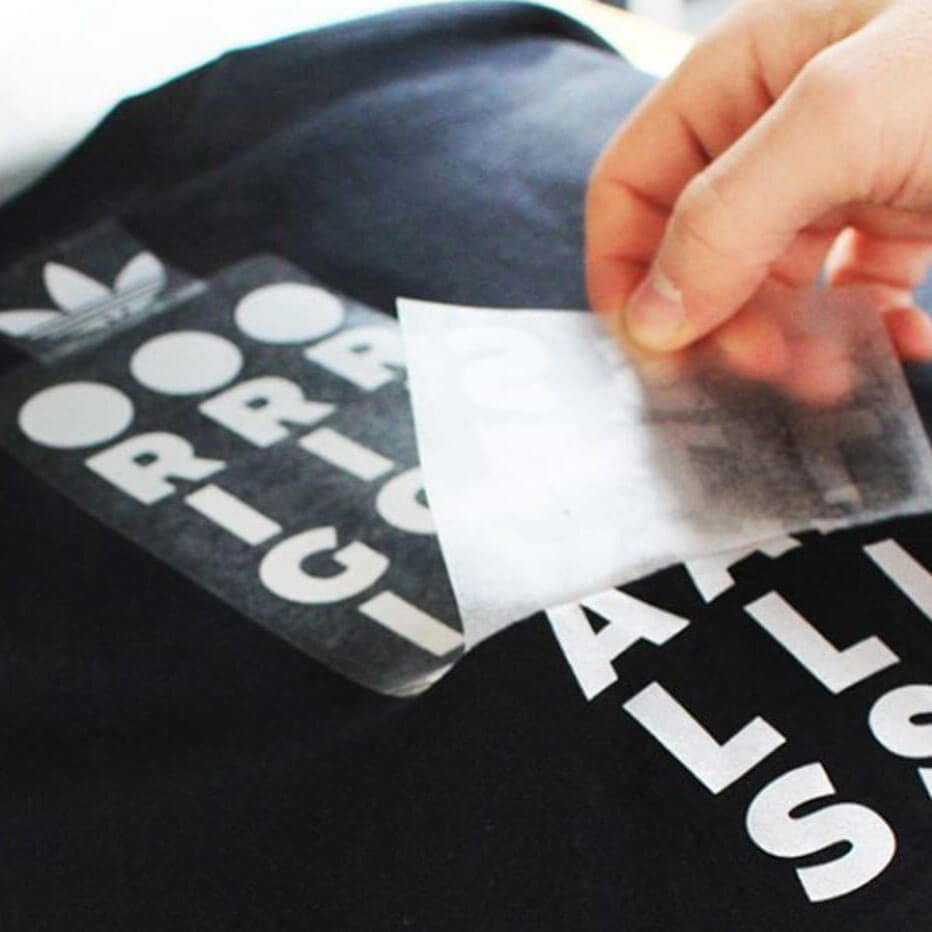
VINYL TRANSFER
This is the process of printing designs onto special transfer paper and then applying the transfer paper onto the t-shirt or garment using a commercial heat press.
It enables full-colour images to be printed very quickly and is a great option for promotional clothing. The downside to this process is that it’s often not as wash resistant as the other three. For more info on this process have a look at our heat transfer page.
SPECIALITY SCREEN PRINTING INK TYPES
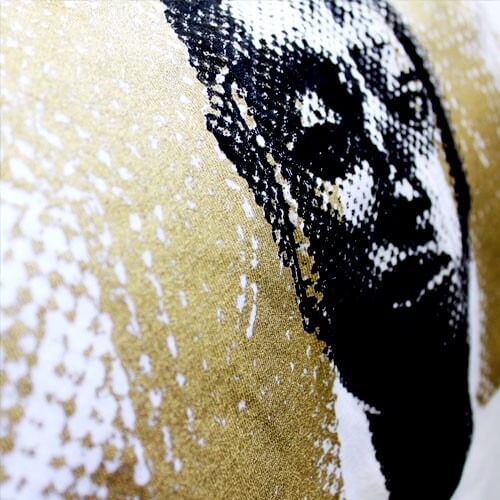
METALLIC INK
These inks are made up of a mixture of pigment and a liquid resin. The pigments have to be ground so that they are fine enough to pass through the mesh of a screen which makes them less brilliant than foiling however the results are longer lasting
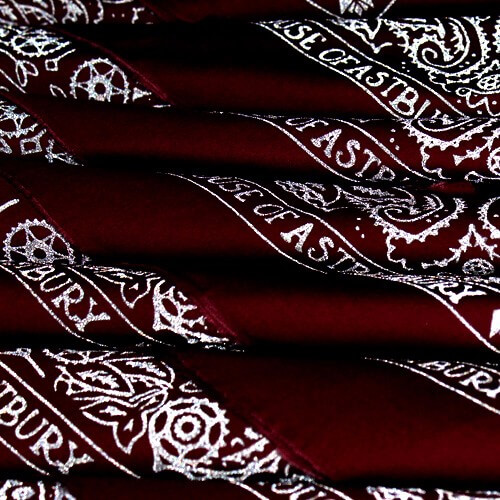
REFLECTIVE INK
Made up of a lycra binder mixed with light reflecting glass beads this ink works really well both as a decorative tool and to increase night time visibility. Really comes to life in front of direct light so the light bounces back.
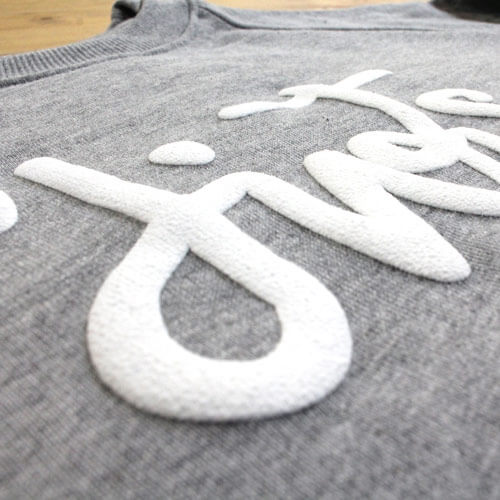
PUFF INK
Chemically designed to puff up when cured these inks become raised when they reach the correct temperature. This process works really well with large and bold designs but also as a final accent colour in a multi layer print.
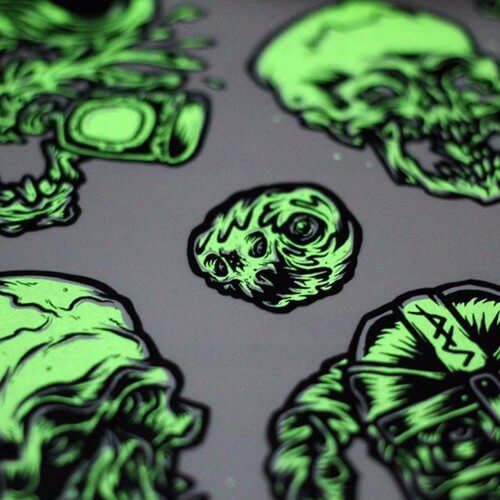
GLOW IN THE DARK INK
Photo luminescent inks owe their magic to phosphors – a chemical that absorbs energy and re-emits it as visible light.
Glow in the dark inks can be produced in a variety of colours but the human eye is most sensitive to green light so this will appear brightest.

FOIL PRINTING
We supply and print a number of different coloured foils for application onto almost any garment. The print process involves us screen printing a glue and then, once the it has cured we heat press the foil of your choice in place.
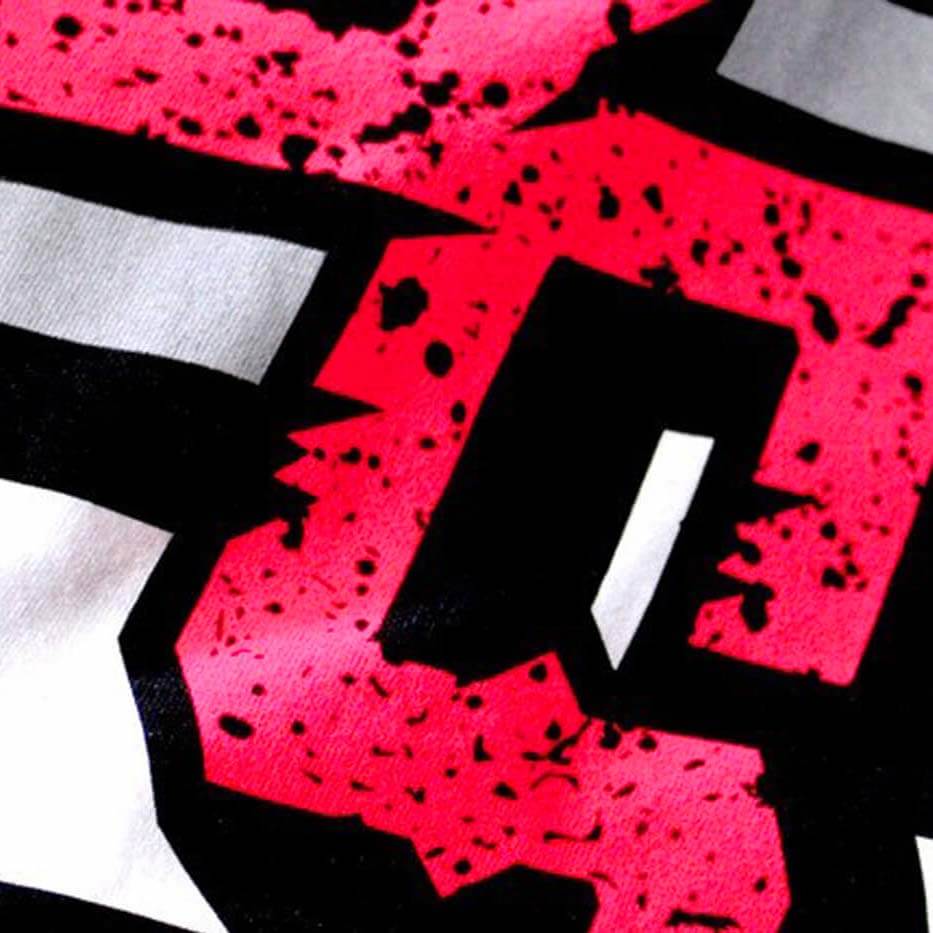
FLOURESCENT INK
The pigment in fluorescent ink works by absorbing UV energy and transmitting it as longer waves. The inks can be fairly transparent so almost always require either a base or double hit but the final outcome is striking, particularly on dark garments.
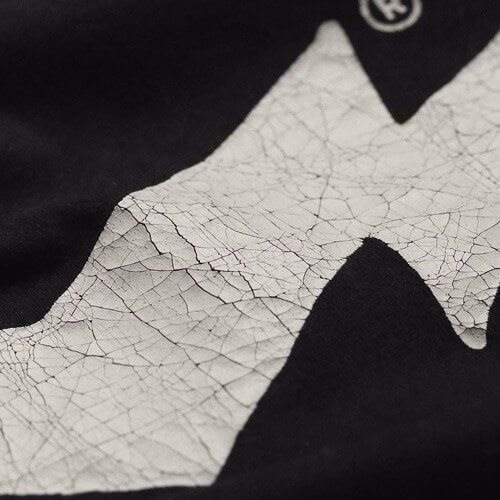
CRACKING INK
This ink is perfect for giving your t-shirts an instant vintage look. A self crack base is applied before the top coat is printed. The heavier the ink application the larger the cracks will appear.
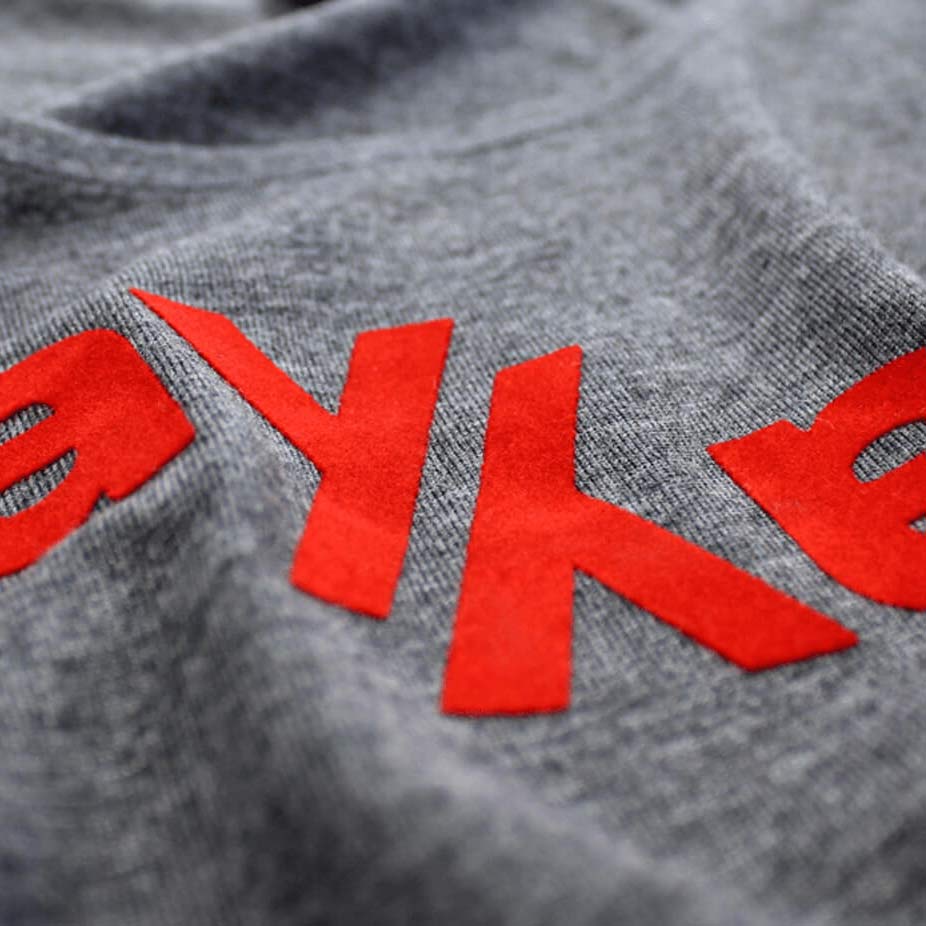
FLOCK PRINTING
Not so much an ink as a transfer flock is a way of adding a soft velour like texture to a design. The process works by first screen printing an adhesive base before applying small synthetic or natural fibres and heat pressing to seal.
COMPLIMENTARY GARMENT CUSTOMISATION SERVICES
Our extensive range of garments, combined with garment finishing and expert embroidery services, seamlessly complement your t-shirt printing requirements. With high-quality blanks and our comprehensive solutions, we make sure your custom apparel vision is realized to your requirements.
3rd Rail provides embroidered garment services in London, your go-to for exceptional garment embroidery. Elevate your collection with expert craftsmanship, from cozy hoodies to chic headwear. Embroidery adds finesse and uniqueness to your style. Contact us to bring your vision to life.
3rd Rail offers an all-encompassing array of garment finishing services. Our services include relabelling, inside neck printing, folding, bagging, and customized tagging. These meticulous touches enhance the overall quality and presentation of your apparel.
Elevate your brand by choosing premium blank garments from industry leaders such as Stanley Stella, AS Colour, and Continental Clothing. Attain the same high-quality standards found in leading high street labels with our exceptional streetwear collection.
GET A QUOTE
PLEASE FILL IN THE FORM BELOW
We’d love to hear from you, so please get in touch with your enquiry so we can begin to process a quote. We offer a sampling service so please don’t hesitate to get in contact with us.